A rail depot is naturally a hazardous environment. The combination of moving vehicles, high voltage electricity and large, powerful machinery all contribute to potential risks in a working environment used by rail and maintenance staff every day.
In the EU depot accident figures often go unreported, in part due to depots being excluded from the key metrics in the Report on Railway Safety and Interoperability in the EU. A lack of data masks the scale of the depot safety problem being faced across Europe.
Where data is available in the UK, according to the Rail Safety and Standards Board’s Annual Health and Safety Report, depots accounted for 23% of all workforce harm in 2022 and 2023, and a third of all fatalities over the course of a five year period. It is stated too that it is likely that there are several incidents or near-incidents that are not reported, which means that the number of near-fatal events is probably higher. As such, depot safety is a key focus for both new and existing depots in the UK.
With an EU-wide focus on rail safety, with particular leadership in countries operating the largest networks such as France, Germany and Italy, there is a clear year-on-year reduction of rail accidents. However, it is remiss to not apply the same focus on depot safety as there is in the rest of the rail industry.
In particular, within the complex environment of a depot an appropriate safety culture must be adopted if human error is to be mitigated and rail personnel are to be protected at all costs.
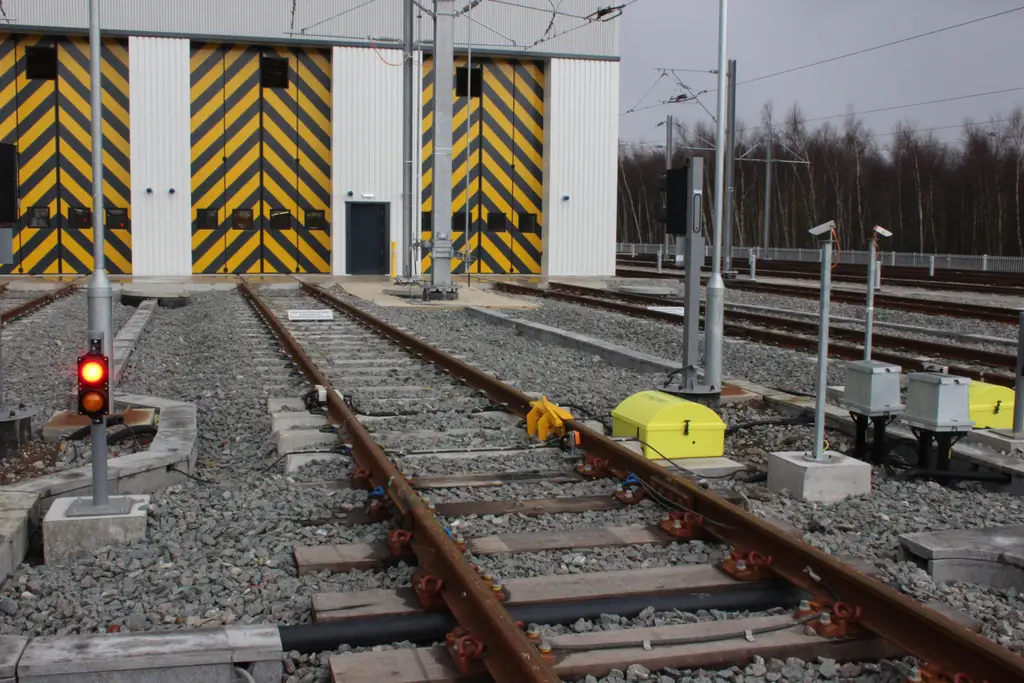
Safety Culture – What is it and how does it prove useful?
What does is the current safety culture model in rail, and what are the systems that can be put in place to ensure a safer working environment in depots?
By definition provided by Solutions from HSE, ‘safety culture is a combination of the attitudes, values, and perceptions that influence how something is actually done in the workplace, rather than how it should be done.’ They continue to include that ‘… Poor safety culture has contributed to many major incidents and personal injuries and can be just as influential on safety outcomes as an organisation’s safety management system itself’.
The assessment of safety culture is key in looking to make tangible change, and in 2019 the European Union Agency for Railways developed the European Railway Safety Culture Model to progress safety change in the EU. It is a conceptual and evaluation framework, which allows for the assessment of safety culture and provides identification of areas where improvement is required.
The model looks at cultural enablers, behaviour patterns and railway safety fundamentals, and states that a positive railway culture is characterised by a united commitment by leaders and individuals to satisfy the four railway safety fundamentals, which are: controlling major risks, understanding workplace reality, learning from experience, and integrating safety consistently. As highlighted, the approach has been shown to work in rail safety in the European Union with clear year-on-year reduction of rail accidents, as seen in the report on railway safety and interoperability, conducted in 2022. As before however, depots are excluded from this information.
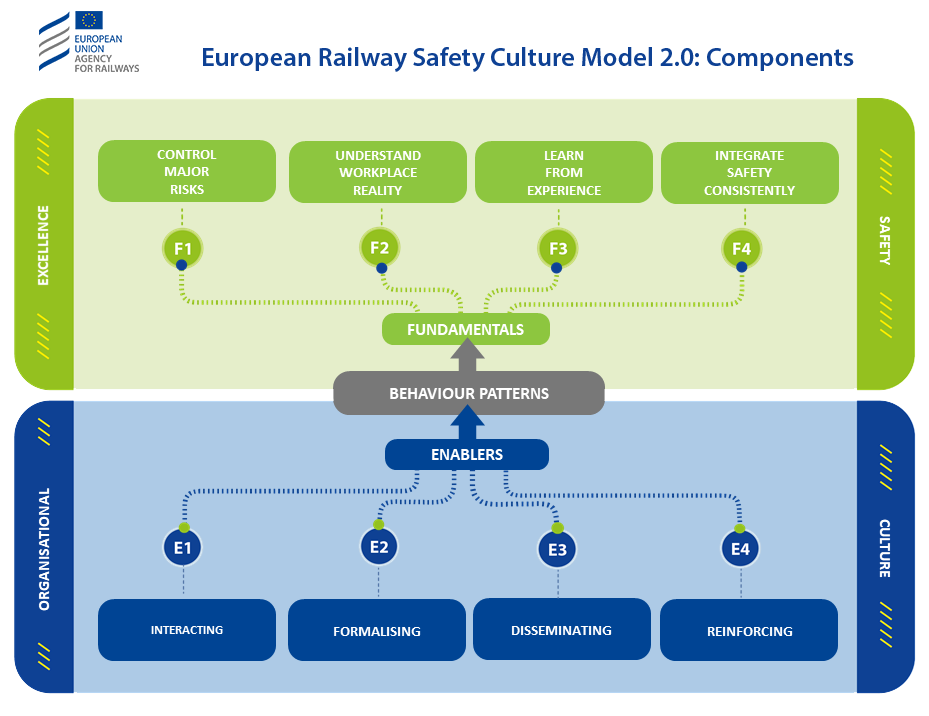
The complexity of depots, with multiple companies and staff having overlapping operations, the required level of focus on safety culture cannot be overstated. In other sectors such as aviation, there have been instances where risk has been assumed to be mitigated by another party, or organising partner, and blind spots in safety have been missed. The aviation safety culture stack here underscores the importance of recognising and addressing dependencies and emphasises the need for robust oversight, transparency, communication, and verification processes to ensure that safety remains a top priority across all entities within the aviation industry. This approach to safety stack and focus on blind spots is key to long term safety in rail depots too.Â
Â
So, while implementation of the safety culture model has shown to reduce the number of rail accidents, it cannot be assumed to be foolproof. The question then is, when it comes to these four safety fundamentals, who can the rail sector turn to? And how can blind spots in safety be eliminated?
Designing Safety into Depots with DPPS
In the UK, the Rail Delivery Group’s Good Practice Guide noted in 2023 that depots, yards and sidings have been deemed the ‘Cinderella of the railway’, despite being crucial to the success of the rail network. The onus therefore falls on operators of rail maintenance facilities to mitigate the unavoidable risks depots workers face daily. Considering these risks and calling for greater investment in good working practices is depot safety specialist Zonegreen, part of Sentric Safety Group.
Zonegreen’s market leading Depot Personnel Protection System (DPPS) helps reduce the risks faced by depot staff by effectively managing the movement of rail vehicles. It is the most advanced, thoroughly tested and proven technology on the market – a product of more than 20 years’ research and experience.
DPPS provides physical protection to depot operatives through the use of powered derailers, controlled by road end panels. Staff log on using RFID tags, which record their location and activate the appropriate derailers. They remain in place until the person has logged off and the road is opened to traffic.
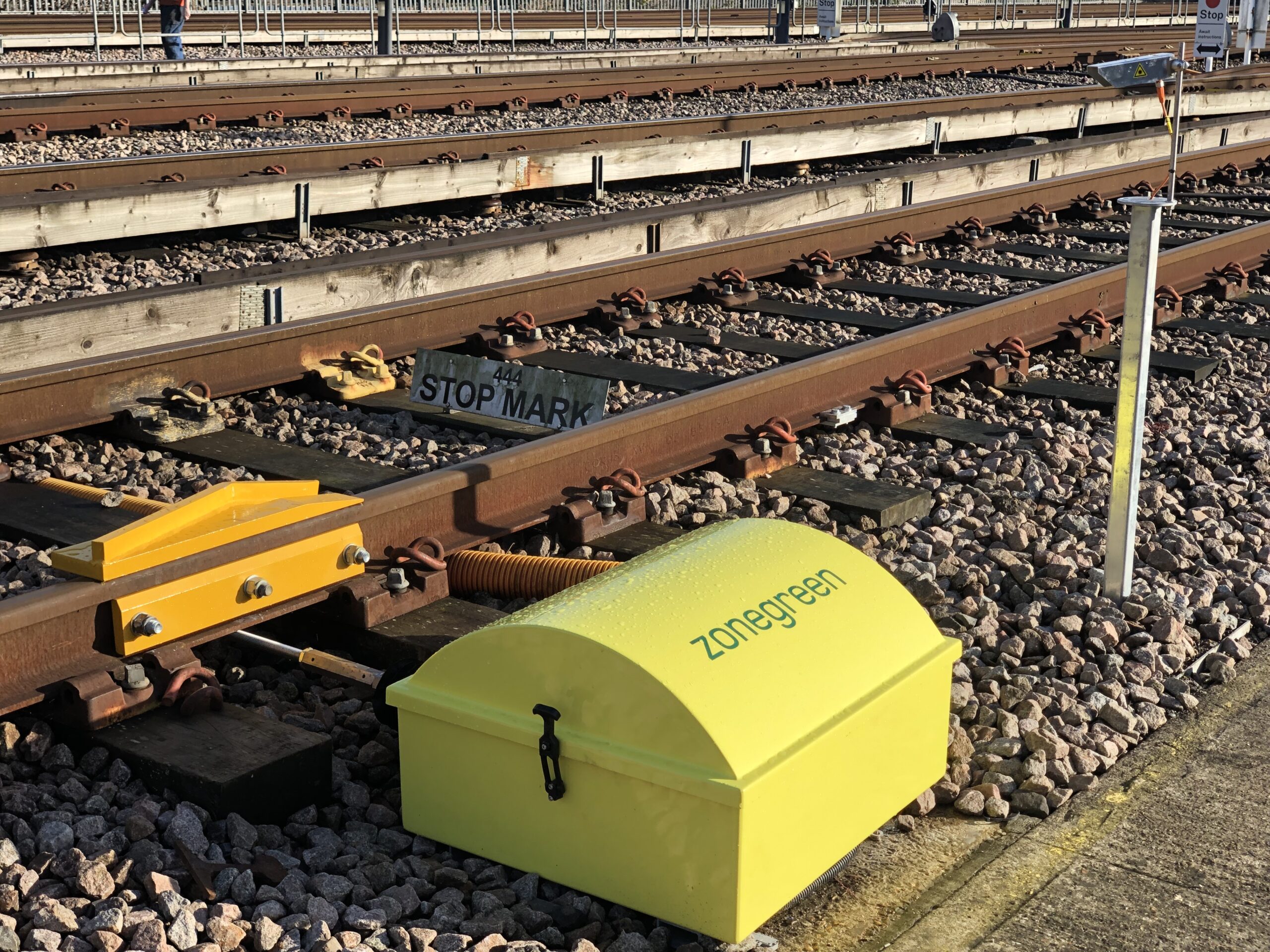
Only when a road is free of personnel can the derailer be lowered and the shunt signal set to ‘proceed.’ Beacons and klaxon which provide audible and visual warnings, are then activated to alert depot staff to imminent vehicle movements. Included in the DPPS package is Zonegreen’s advanced Depot Manager SCADA software, which offers an overview of the entire protection system and complete traceability. It displays the location of personnel and the status of plant and equipment, whilst providing key information to make operations easier and quicker to implement. For example, the technology can identify peak movement times, so additional focus can be placed on safety during these highest risk periods. DPPS boasts independent certification to prove its compliance with both the hardware and software requirements on SIL 2; a reliability assessment of the relative risk reduction provided by a safety system.
DPPS – An Imperative
Zonegreen’s DPPS is designed to minimise the consistent risks faced by depot workers. By automating safety procedures and ultimately reducing the risk of human error, one of the main causes of accidents, DPPS has been established as one of the most advanced systems on the market.
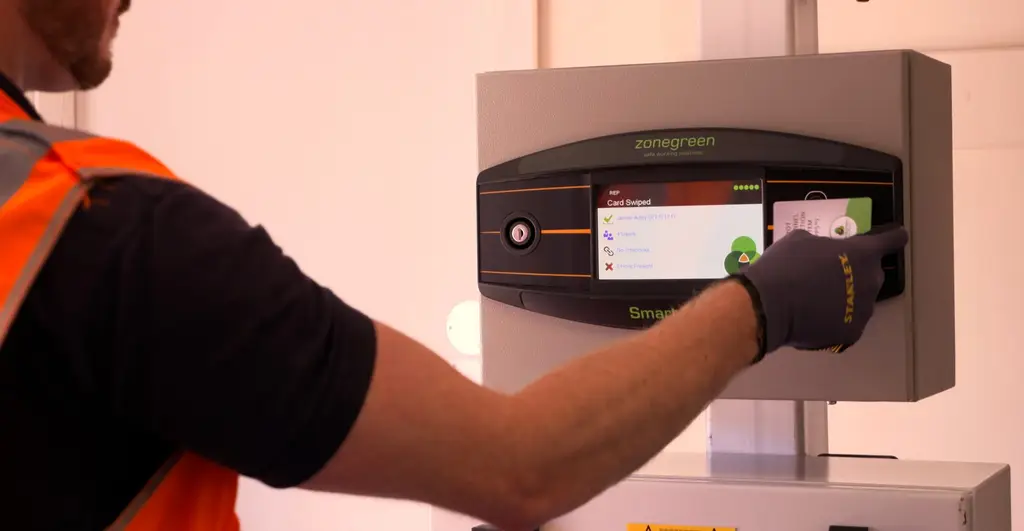
Modern electronics used to reduce cabling and electrical components have ensured that DPPS is not only more resilient and easier to install or expand but can allow for future upgrades.
All these factors contribute towards a system which fundamentally changes the way in which rail depot personnel safety can be achieved across rail depots; demonstrated in the dozens of DPPS installations worldwide.
For more information about Zonegreen’s DPPS safety solution, please read more at https://www.sentricsafetygroup.com/applications/rail-depot-safety-solutions/ and get in touch.